TLX series
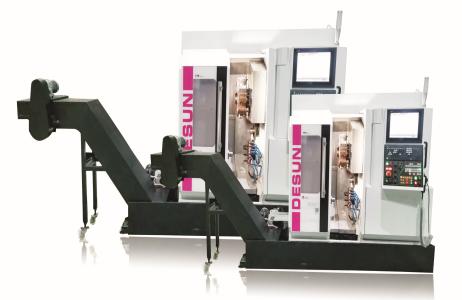
High-efficiency processing production unit
*TTLX series is a small/medium/large turning compound center launched by DESUN Company. Since its launch, this type of machine tool has sold hundreds of sets. Since its launch, TLX has emphasized the high rigidity and high precision turn-milling compound machining of machine tools. Its high stability processing is praised by a wide range of customers.
*TLX series is our positioning mid-range mass production machine tool. Its flexible configuration is suitable for enterprises of different scales and industries. Whether it is small parts processing or large parts processing, TLX series can meet the requirements. TLX series can not only be produced by single machine, but also can be used to improve efficiency by connecting bars. TLX is a full-functional design scheme with two spindles and one turret+Y axis. Each axis adopts 35-type roller guide rail to ensure the highest rigidity of the machine tool, including the best dynamic response and high-strength base shock absorption. At the same time, it also brings about the extension of tool life, the improvement of surface smoothness of parts and the reduction of workpiece beat and processing time.
TLX series has rich configurations, and the specific models are as follows:
- TLX-300 series small turning compound center
- TLX-500 series compound center for turning medium-sized cars
- TLX-800 series compound center for turning medium-sized cars
- TLX-1250 series large turning compound center
Machine Tool Design Concept and Optional Accessories (Option)
* TLX series is the most comprehensive model developed by Seiki, covering 80% of the market demand for horizontal lathes.
* Bar diameter, standard configuration ∅Φ 30 mm/Φ 42 mm/Φ 52 mm/Φ 65 mm, depending on the spindle size.
* One high-power spindle is provided as standard, and the motorized spindle can be configured for Type 30, Type 42 and Type 52, and the mechanical spindle is provided as standard for Type 65 spindle.
* TLX-300/500/800 series adopts BMT-45-16T servo power turret, which can install 16 different cutters.
* TLX-1250 and TLX-1500 large machine tools adopt BMT-65-12T heavy servo power turret.
* TLX-1250 and TLX-1500 can choose to install the center frame (Option).
* 5"6"8"10"12"15"20 "inch chuck (Chuck & Spindlie Option) can be selected for all series spindles.
* High-quality and high-efficiency back machining can reduce the loss of workpiece precision caused by repeated clamping.
* High-speed moving, TLX-300/500/800 is 45 meters, (TLX-1250 and motorized spindle have high-speed response, and the C axis is divided by 0.001 mm.
* Simultaneous rotation and docking of double spindles, rapid rotation and positioning of double C axes, and high-rigidity milling are the standard configuration functions of TLX.
* DESUN Seiki standard is matched with Mitsubishi M80 system of Japan, which supports all ultra-precision turning and milling functions except five axes.
Introduction to the functional advantages of TLX series centrifuges
* The machine tool adopts double spindles, double C axes, single turret and single Y axis, with powerful functions and excellent performance.
* Because the machine tool has good stability and rigidity, the tool life is long, for example, the tool life is increased to 38% compared with the earlier machine tool.
* The diameter of the X-axis lead screw reaches 40 mm. Under long-term high-speed operation, the large-diameter lead screw ensures the precision and service life of the machine tool.
* P-class 35mm roller guide rail is adopted to ensure long-term high-efficiency heavy cutting task.
* TLX series small machine tools are driven by motorized spindle, with fast response, low failure rate and easy maintenance. Large machine tools use mechanical spindles.
* Standard configuration of 20Bar high-pressure system ensures that the machine tool can easily deal with deep holes. (40Bar high-pressure system Option can be selected)
* Fully automatic receiving hand is equipped with standard configuration, so that after the processing task is completed, it is automatically taken out by receiving hand and placed in the finished product box. Real unmanned processing.
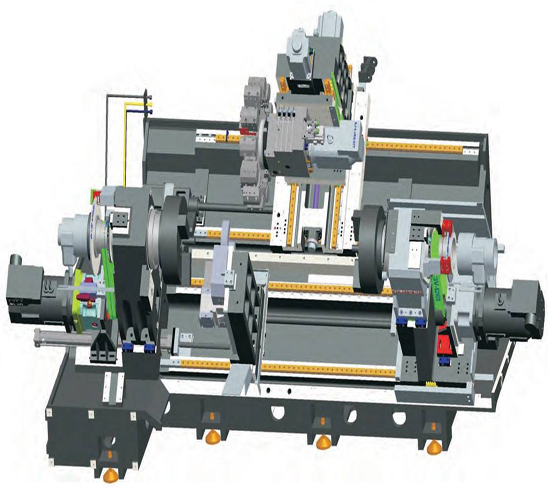
Machine tool design
TLX series is analyzed by advanced finite element technology. After repeated verification, it achieves high rigidity and lightweight fuselage. This model adopts all roller guides. Compared with the traditional ball guides, the roller guides have the excellent characteristics of smaller elasticity relative to the load. By assembling a large number of roller bodies in the sliding unit, the rigidity can be several times higher than that of the ball guides. Orthogonal Y-axis, using its straight-forward characteristics and high-speed feed, can realize efficient machining, and using the structure with excellent rigidity, can realize the same or even higher machining accuracy as the machining center. As a new type of compound processing machine beyond the scope of turn-milling compound center, it has excellent turn-milling processing ability.
Machine tool design considerations
The high rigidity of the machine tool is the key to determine the later application accuracy of this machine tool. German engineers first consider the application of cast iron when developing the machine tool. The internal structure design of cast iron ensures that the machine tool is not easy to be thermally deformed in the later high-speed machining, and the vibration of the machine tool is also the main reason that affects the product size. In the research and development, engineers fully consider the later application scenarios of the machine tool and try to summarize and pay attention to the unfavorable factors. The excellent performance of TLX series machine tools with high precision and high stability perfectly reflects the German engineers.
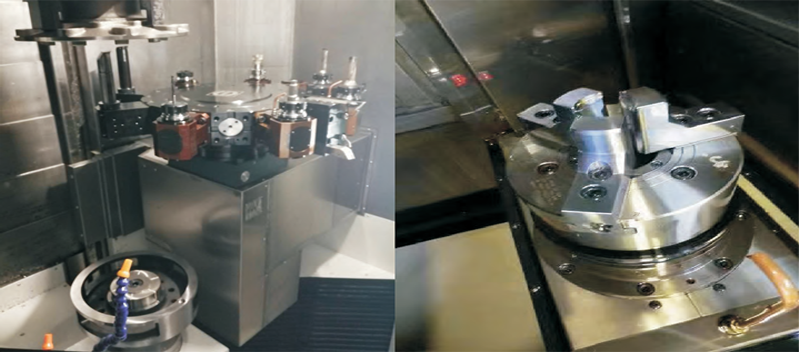
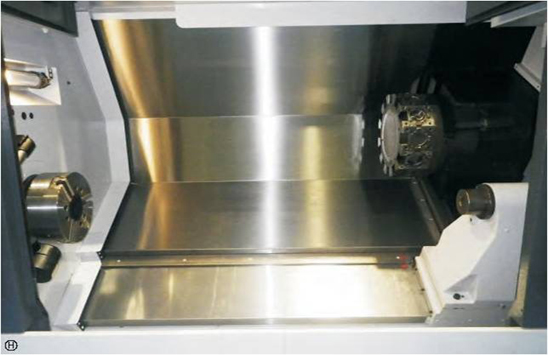
Intelligent cooling system

* Electrical cabinet air conditioning, TLX standard full range of electrical cabinet air conditioning, to ensure that electrical appliances and drivers work stably in a constant temperature environment for a long time.
* Cutting fluid air conditioner, TLX series full range standard configuration cutting fluid air conditioner, aimed at cutting fluid constant temperature, so that workpiece processing will not change because of cutting fluid temperature change (Option).
* Electric spindle oil-cooled air conditioner, TLX series full series standard configuration spindle oil-cooled air conditioner, to ensure that the spindle works for a long time, the spindle temperature is kept in a reasonable state, and the spindle precision is improved.
* The hydraulic station is equipped with oil suction (oil outlet) filter and oil return filter as standard. When the machine tool runs for too long, hydraulic oil is circulating, and hydraulic oil is mixed with scrap iron because of normal wear of the machine, the pump of the hydraulic station is well protected by the filter.
* The hydraulic oil pipe is upgraded from the original rubber pipe to galvanized steel pipe to ensure that the oil pipe will not age after many years of machine tools.
* 40Bar high-pressure system can be configured to ensure that the machine tool can easily deal with (Option) when processing deep holes.
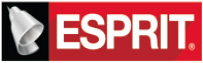
Simulation and verification
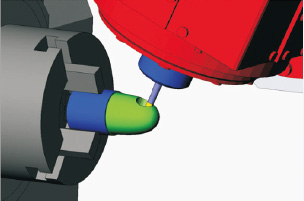
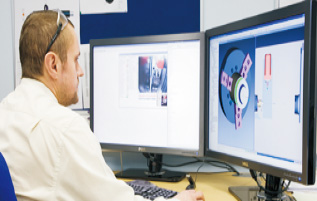
ESPRIT intelligent programming solution, ESPRIT-CAM software enables you to simulate tool processing on a machine tool through a 1:1 machine tool model in a computer through ESPRIT software before cutting, so as to find tool interference in advance, take measures to avoid machine collision due to tool interference, and reduce the loss caused by maintenance and shutdown of enterprises due to carelessness or ignorance of machine tool performance. ESPRIT software can solve the problem of easy to learn, intelligent generation of machining tool path and quickly calculate complex tool path, reducing errors. Users only need one system to complete the programming of turning-milling compound machining. The operation interface of the software is friendly and easy to learn. Interference prevention simulation function. Machine tool collision prevention function. Comprehensive man-machine dialogue function and intelligent programming.
We recommend to choose a set of such software, which is very necessary for programming multi-axis compound machine tools in production! For the huge loss caused by programming efficiency and programming misoperation, a set of software is worth investing!
Nidec Co.,LTD MP ruler is a strategic partner of DESUN Company, and DESUN Company configures MP synchronous ruler (grating ruler) in the X-axis standard of all its products.
From a highly integrated operating system, it is convenient for customers to useThe whole series adopts Japanese Mitsubishi high-end series -M80Focus on production and control-including future industry 4.0
*High-speed, high-precision contour control function;
*Hydraulic turning, rigid tapping, hydraulic milling and hexagonal turning functions;
*Virtual and development functions, plane collision prevention, real-time mode;
*Tool R angle compensation function, tool wear compensation function;
*Spindle-vice spindle C axis synchronization detection, rotation synchronization detection, docking synchronization detection;
* Multi-channel (3) independent processing function;
*Taper circular processing, non-circular processing function;
*Chamfering and R-angle turning function;
*Internet wireless link remote diagnosis function.
Strengthen lathe function
The functions of milling and multi-axis and multi-system control are greatly strengthened.
In addition, it also improves the on-site maneuverability and can carry out more complex processing simply and efficiently.
Turning machine
Automatic lathe
Vertical lathe
Inverted lathe
Compound processing machine
More complicated processing can be performed simply and efficiently.
It is equipped with rich functions to support high productivity. By supporting high-speed and high-precision control and SSS control, the milling function is enhanced and the multi-axis and multi-system control function is enriched. In addition, it has greatly improved the functions frequently used by field personnel, such as tool correction and workpiece coordinate system compensation, greatly improved the usability of programming, and can easily carry out various more complicated machining.
Milling function
High speed and high precision control /SSS control
Servo spindle motor control
Functions for Large Lathe
Re-tapping and spindle ratio
Real-time adjustment
Large display
Programming of dialogue mode
Multi-system waiting program editing
Dialog mode insertion loop instruction
3D program checking
Multi-axis multi-system control function
Maximum support: 8 systems, 32 axes and 8 spindles.
Loader control with subsystem control
Spindle overlap, multi-spindle synchronization
On-site handling
Workpiece coordinate system compensation
Can simply set the restricted area inspection parameters.
Can switch to a condensed picture